Epoxy Floor Coatings are a hot and confusing topic in the flooring industry. There is a lot of information about epoxy and about concrete, much of which is misleading, so where do you start? What product is right for you, how do you apply it and are there any prior preparations or considerations you need to make? How do you even know who to trust to give you good information?
The fact of the matter is that plenty of businesses will be keen to sell you a flooring system that will fail; as long as they get paid, they don’t care what else happens. They will make you sign on the dotted line, absolving themselves of any liabilities on their part and then they disappear, leaving you with the cost of removing their terrible workmanship and reinstalling the floor you wanted. It’s a nightmare, and at Hawk CFC, we have heard this story too many times to stay quiet about it.
Below are some key questions you need to ask yourself before ringing around for quotes as well as some key questions for the businesses you request quotes and advice from. These questions will help you to determine where all the costs will be coming from and how much time and effort you can expect will be needed to install your new floor.
KEY QUESTIONS TO ASK
1. What’s on the floor currently?
Before you even begin to think of your final look, look first at your current flooring. If you currently have tiles, vinyl or paint on your concrete, this will need to be either removed completely or ground back to be level and rough or porous enough for the epoxy floor coating to create a permanent bond with the substrate. Bear in mind, too, that removing tiles and other coatings can easily leave divots in the surface that will need to be repaired before it is re-coated. These repairs will always show through if you finish the floor with a clear sealer or polishing.
2. Is the condition of your concrete suitable for an epoxy floor coating?
A common misconception is that all concrete is equal, and nothing could be further from the truth. If you have ever baked a cake or bread, you will know that following the recipe down to a T does not guarantee that your cake or loaf will turn out exactly the same as the picture in the recipe. There are many, many conditions that affect the final outcome of the surface, which ultimately affect the final epoxy floor coating, such as temperature during curing, the temperature after curing, moisture levels beneath the surface and in the air, the mpa compressive strength, the materials used within the slab, the workmanship of the people who poured it and the amount of movement the slab experiences – among many other things! The surface hardness can affect the polish-ability, concrete under 23-25 mpa are more difficult and do not always achieve the desired result- however, fear not, if this is what you’re after, there are always options for you! (See our Insitu Spaces – Original Series). ERFLA also have a system designed to polish low grade concrete – talk to us about the options.
So here are some guides on things to look for in your surface before you can even begin to think of the final epoxy floor coating:
- Are there any visible cracks or divots in the floor? With clear coatings and polished concrete, you will have 2 choices, have the cracks highlighted to a colour, or leave them as they naturally are – concrete is a beautiful natural colour even with some cracks. For resurfacing systems, a high grade crack repair is performed prior to flooring installation to minimise the chance of the cracks reoccurring.
- Has any moisture, oils or other liquids penetrated into the surface? Sometimes there are visible stains as a result.
- Are there expansion joints in the slab? Are you hoping for them to be filled in with the finished product? Not all expansion joints should be filled in.
- Is there obvious height differences on the floor? Using a 2m level on different areas of the floor is a quick way to answer that question.
Treating these kinds of issues in the surface is not automatically included in the cost of laying an epoxy floor coating. Be aware that you may receive a quote for laying an epoxy floor coating, only to find the price increases later when the installer discovers issues in your surface. These new costs will be covering the cost of extra materials and man-hours required to ensure the finished floor will not fail on account of a poor quality slab. It’s only natural to be suspicious when this happens, but you should be more suspicious if your slab shows any of the above conditions and the installer does not address them; in such cases, they have likely ignored the problems and just proceeded with the flooring installation, which will come back to hurt you long after the installer has left.
3. Is the concrete slab level with the rest of the flooring?
There are a few occasions when the slab is lower than the flooring in neighbouring rooms/areas by 10mm or more. This can be the result of old flooring being removed, or if the property is a new-build with allowances for screeding and falls to drains in a wet-area, or sometimes it is just the result of an older property that was built in a time with different building standards. In such cases, the floor can be built up to be level with the rest of the floor by means of floor-levelling or screeding. This will be an additional cost to the flooring installation, so be sure to mention it when requesting quotes so that all information is upfront from the beginning.
Be aware also that there are flooring options that incorporate floor-levelling and a finished epoxy floor in one sweep. See ERFLA Insitu Spaces – Original Series as an example of a resin flooring system that can also behave as a floor-levelling system at the same time.
4. How are you going to prepare the floor for permanent adhesion of the final epoxy floor coating?
There are several different ways you can prepare your surface for a coating to be laid on it; but one way that is never an option is no surface preparation at all! Not every form of surface preparation is appropriate in all situations. Sometimes even the highest quality option is too aggressive for your personal situation, and many times the gentlest and cheapest is not aggressive enough to ensure your finished product does not de-laminate. Of course, if you are wanting polished concrete, this is the most vital question of all! Some options for floor preparation include the following, from lightest to most industrial:
5. What area is your floor?
Get at least a rough m2 of the size of the are to be coated. If you don’t have the right equipment, or don’t know how to measure your floor, you can follow our simple guide ‘How to measure your floor’ for assistance. When receiving final quotes on your flooring, someone should visit your property to properly measure for themselves and visually inspect for any concerns. Proceed with caution if this is not the case.
6. What’s your budget?
This is often the number one thing on people’s minds when obtaining a quote. Always remember that in this industry, price reflects performance and longevity of the product. Be very cautious of epoxy coatings and paints that come with a stock-standard price per square metre. While this is exactly the kind of information everyone wants, the complexities of installing a chemical-reactive flooring makes it practically impossible to have any kind of ‘one-size-fits-all’ option. If you choose the ‘off-the-shelf’ option, you will probably save a few dollars now, but will not gain the longevity and performance of a permanent coating system. If you’re playing a long-game, the customised quotes are the ones you’re looking for.
Check out our page ‘Epoxy Floor Cost‘ to see some of your options.
7. How is your epoxy floor going to be used?
What is your intention for the long-term use of the floor? The great thing about the floor coatings such as epoxies, polyurethanes, polyaspartic, poyurea and Methyl Methacrylate (MMA), is that they are highly versatile and can be customised to suit your requirements. These requirements will affect the kind of floor coating you need. Some of the main questions you need to ask are as follows:
- What kind of foot/vehicle traffic are you expecting? The higher the traffic, the more hard-wearing the resin needs to be.
- Do you need your floor to be food-safe or HACCP Accredited?
- Will there be strong chemicals dropping on the floor?
- Do you require the floor to be non-slip?
- Will you need safety or line-marking?
- Will there be direct sunlight hitting the floor, even through a window?
- Will the floor come into contact with high volumes of water, such as wash-downs or rain?
- Are there drains? Do they have falls or do you require falls to drains to be created? How many drains are there and what kind of drain are they?
All of these factors affect the amount of resin that will be required (particularly when it comes to falls to drains), which additives need to be included, and ultimately which type of resin you need because not all additives play nicely with each other. Sometimes these additives can come free of charge, but don’t necessarily come stock-standard, so make sure you articulate these things clearly.
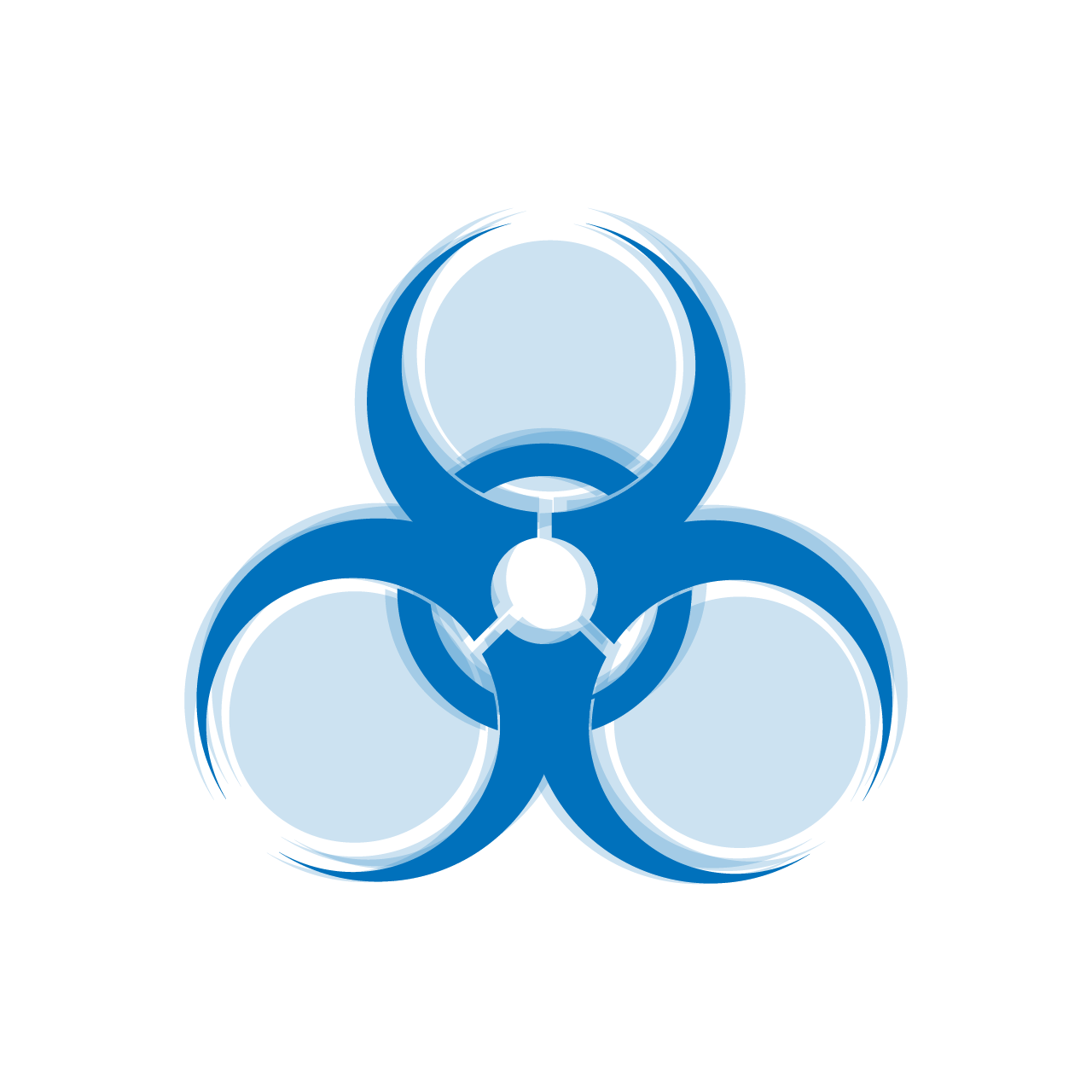
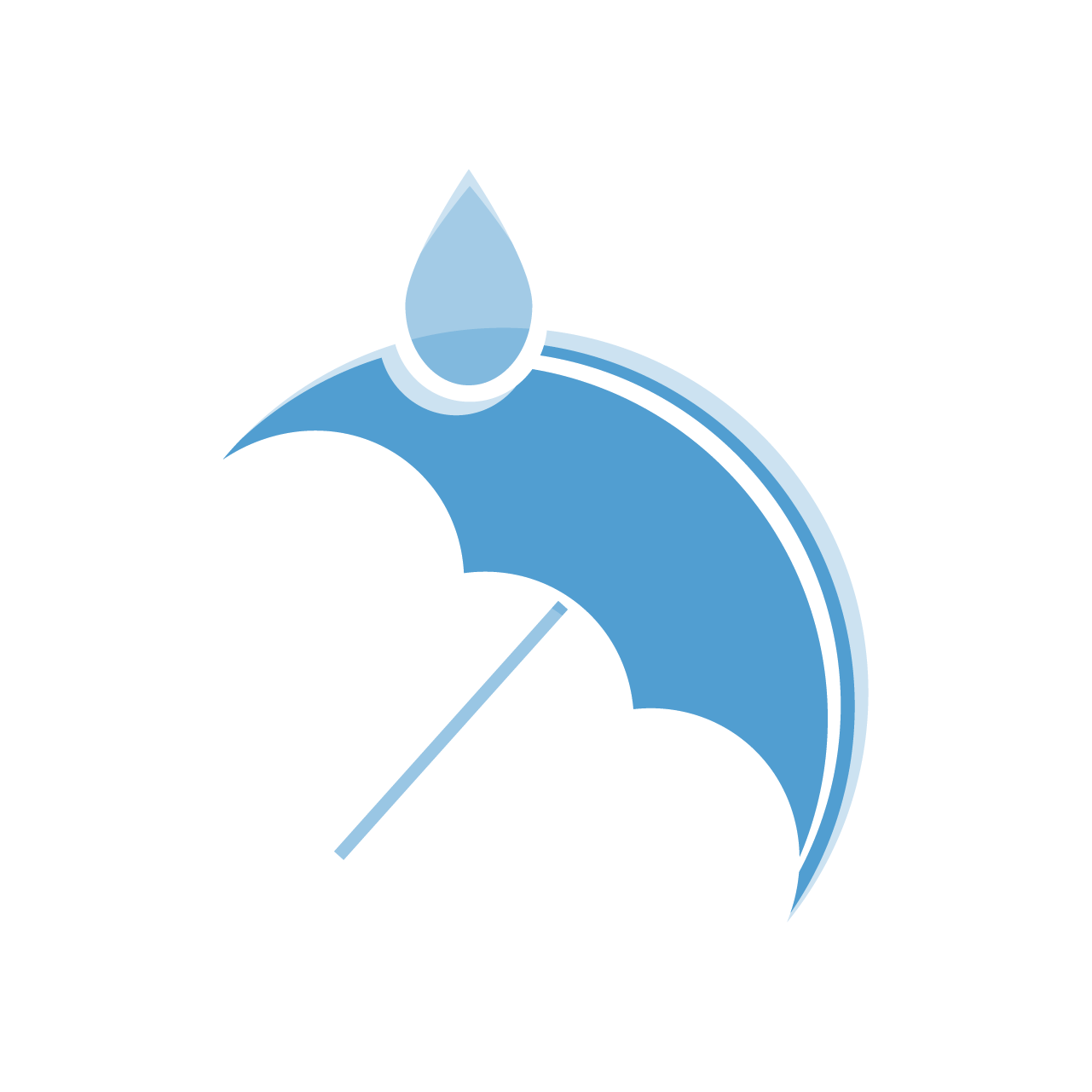
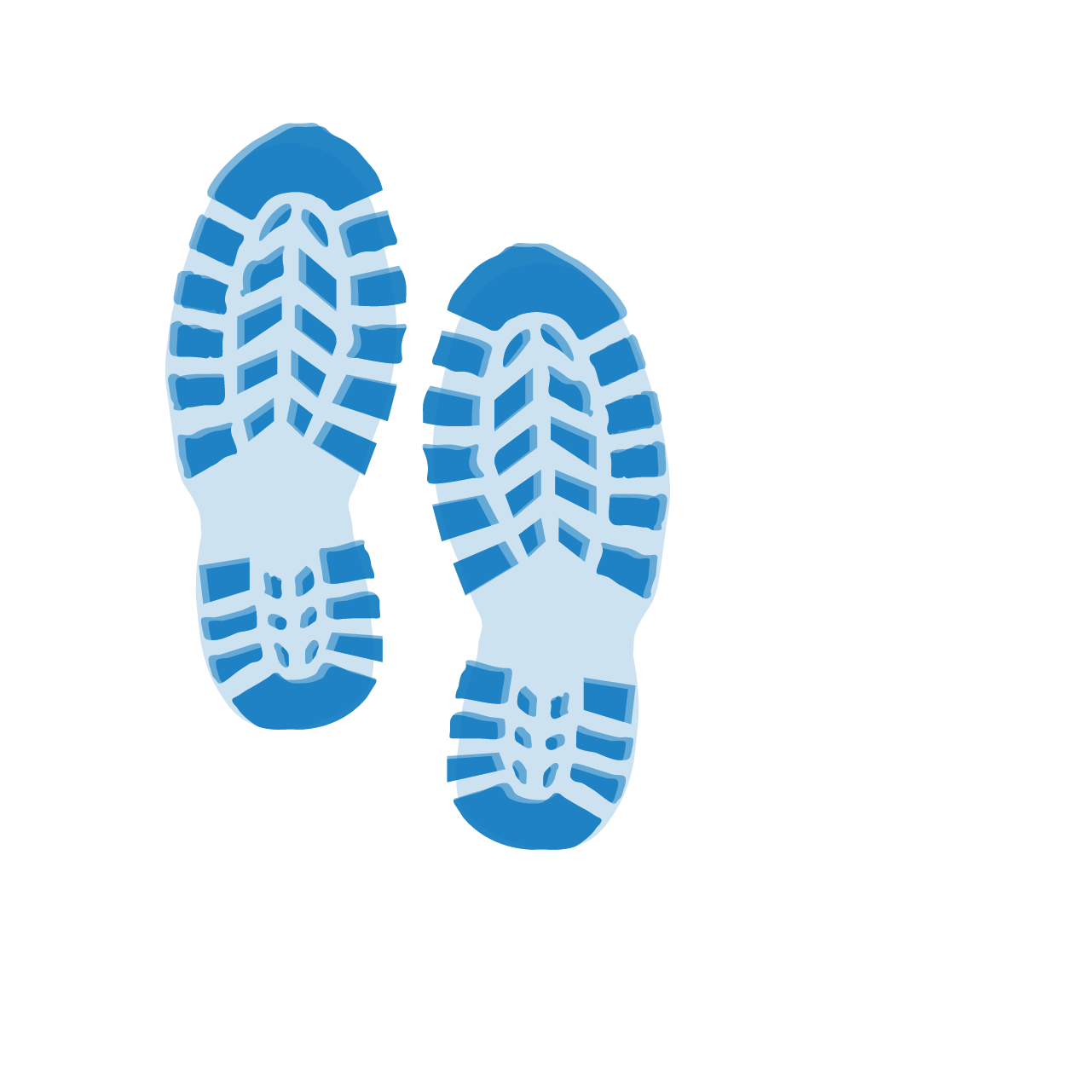
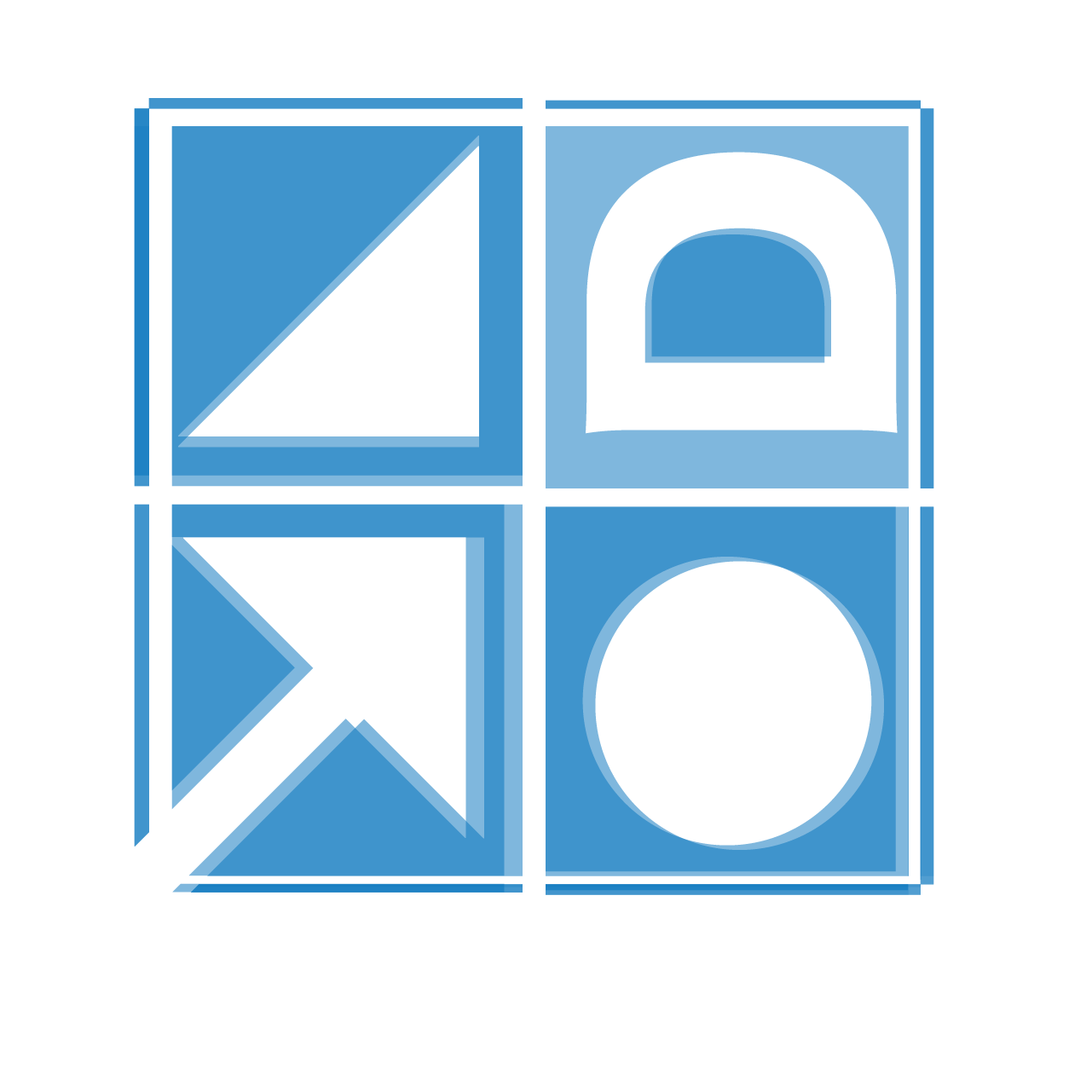
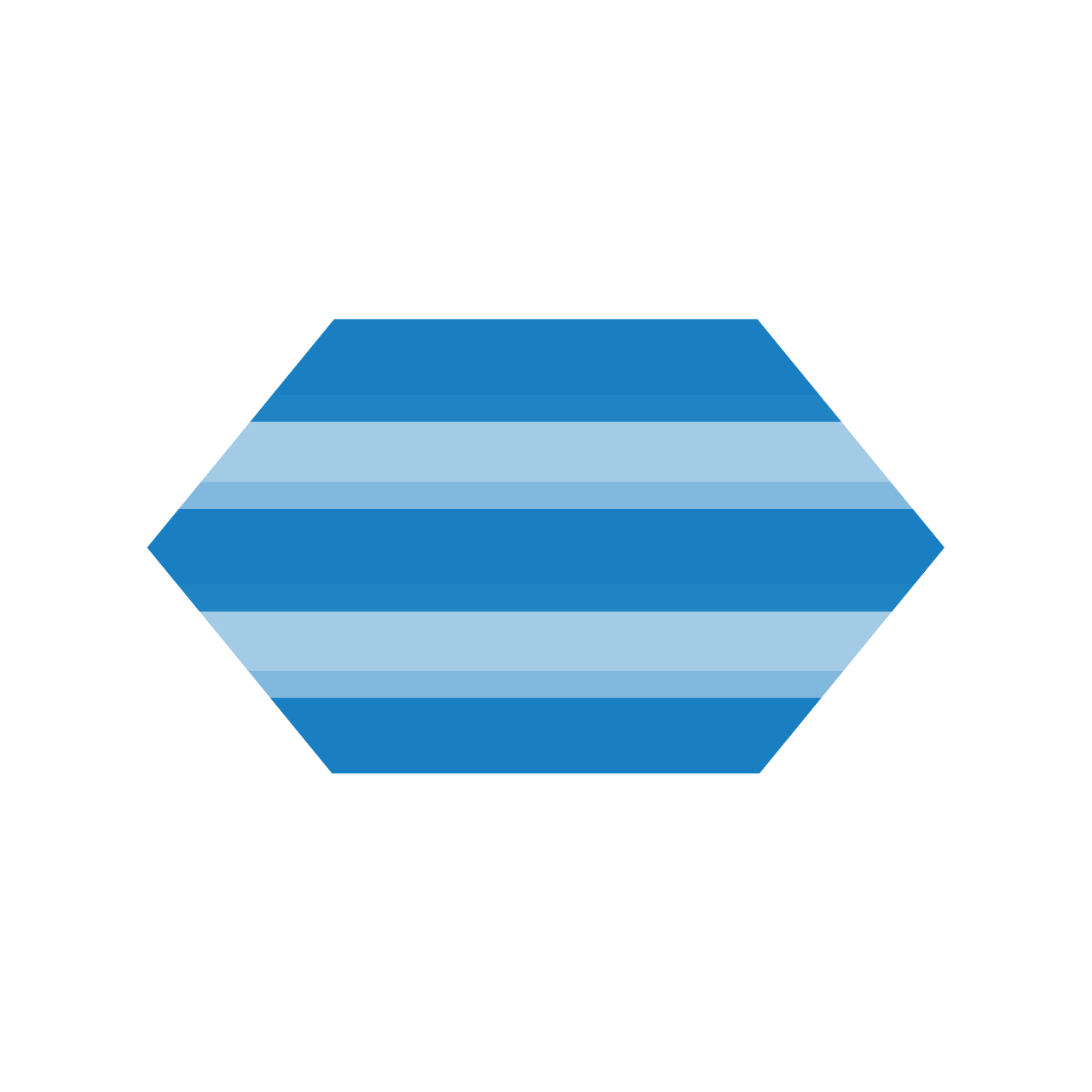
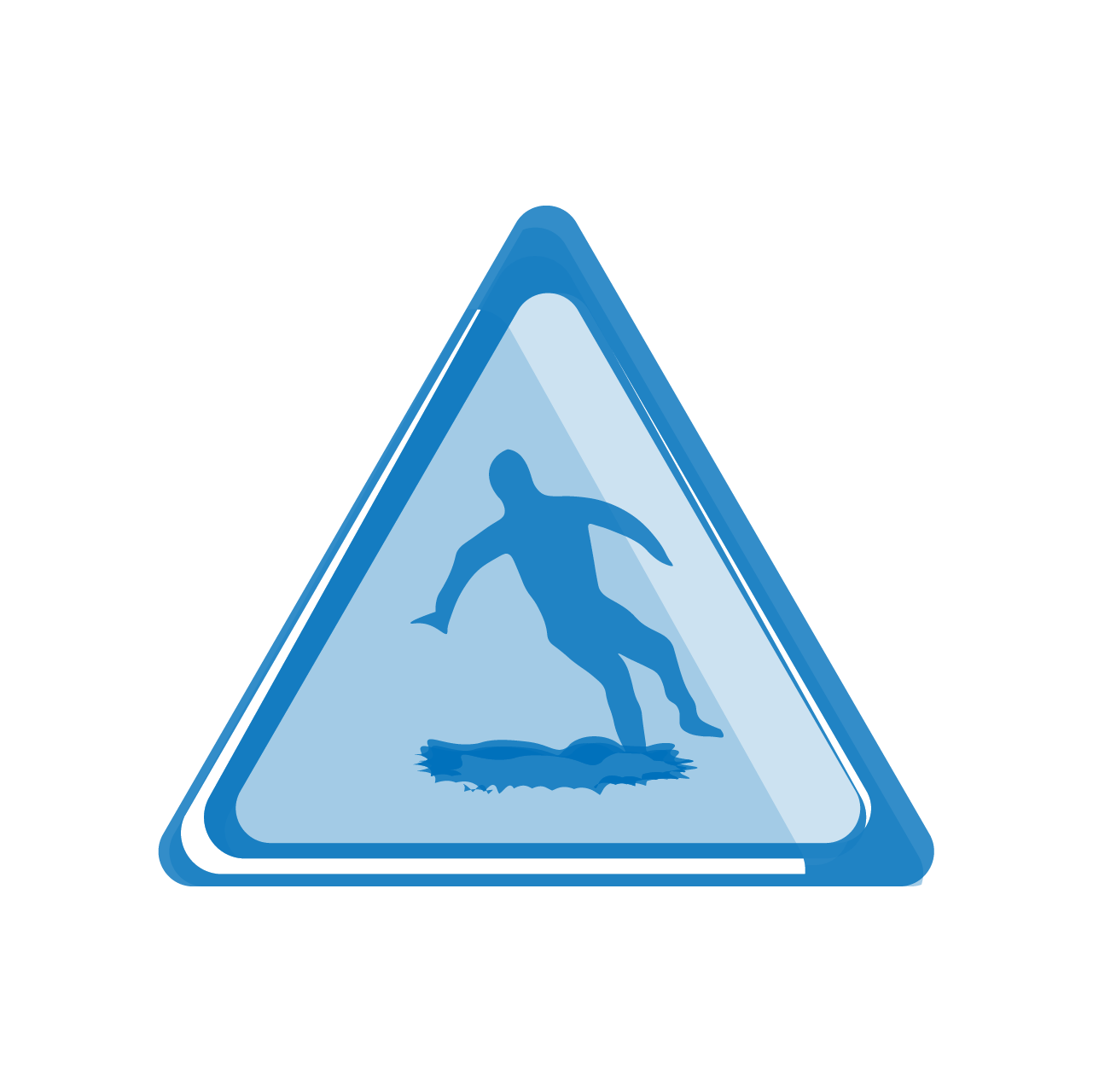
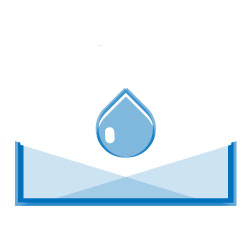
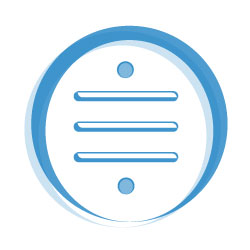
8. How much down-time can you afford?
The more time you can afford to shut down your space, the more options there are available to you. For some people, a total shutdown is completely impossible. If this is you, never fear, in many cases, there are overnight, INSTANT return-to-service options where the installers will be in and out like ships in the night. For everyone else, take curing times seriously. Some coatings may take a week to fully cure, with light use after a few days. Others, such as rapid-curing resins, can take as little as 1 hour. If you ignore the times given for curing, there is no warranty against ignoring the factory instructions. The installer may be able to return and patch affected areas in such circumstances, but even so, as it is a seamless floor, you will always be able to see the areas that have been patched. Therefore, the easiest way to avoid this kind of setback is to strictly follow the curing guidelines for paints and epoxy resins, ensuring you have allowed enough downtime.
9. Do you want a simple Performance Floor or a Designer Finish?
Resin floor coatings come with a myriad of finishing touches that, in many cases, don’t require a compromise on performance to achieve a stylish and sophisticated finish. Many people are only interested in a mono-colour, highly cleanable, low-maintenance, performance floor, and for all of those in need of this, you have a plethora of choices at your fingertips! See our flooring options for various industry Sectors and Commercial Floor Coatings
If you are more interested in a stunning designer floor, you also have many options to choose from. See our designer range of flooring. In our experience, the designer finish that is often most disappointing is the mirror-like, high-gloss flooring. High-gloss floors look incredible, as though you could fall right into them, but they are very high maintenance. For an upmarket hotel or boutique shop that has a full-time maintenance employee to keep the floor up to standard, this floor is still a great option. For your average residence, cafe or any other establishment that does not have the time or resources for this kind of maintenance, matte and satin-finish floors will retain their original beauty for a fraction of the time and cost in maintenance.